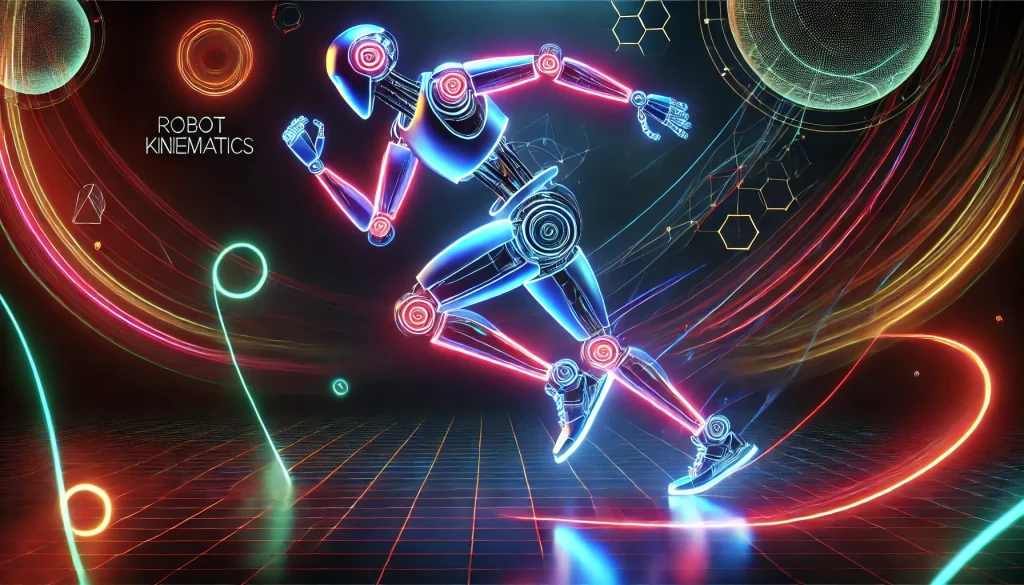
Robot Kinematics: Understanding How Robots Move
Robot kinematics is an intriguing field that delves into the mathematical and mechanical principles governing the motion of robots. Whether you’re a college student, a young professional, or just someone fascinated by robotics, understanding kinematics is crucial to grasp how robots perform tasks, navigate spaces, and interact with their environments. This blog will explore the fundamentals of robot kinematics, breaking down complex concepts into digestible pieces. So, let’s embark on this journey to uncover how robots move and operate!
What is Kinematics?
Defining Kinematics
Kinematics is a branch of mechanics that focuses on the motion of objects without considering the forces that cause this motion. In robotics, kinematics involves studying the movement of robot parts, particularly the joints and links that compose a robot’s structure. By analyzing kinematics, engineers can predict the position and orientation of different parts of a robot at any given time.
Types of Kinematics
There are two main types of kinematics: forward kinematics and inverse kinematics. Forward kinematics involves determining the position and orientation of the robot’s end-effector (the part of the robot that interacts with the environment, like a gripper or a tool) based on given joint parameters. Inverse kinematics, on the other hand, focuses on finding the joint parameters required to achieve a desired position and orientation of the end-effector.
Forward Kinematics: Calculating Positions
Understanding Forward Kinematics
In forward kinematics, we start with known joint parameters (angles for revolute joints or displacements for prismatic joints) and compute the position and orientation of the end-effector. This process is relatively straightforward for simple robots but can become complex for robots with multiple degrees of freedom (DOF). Degrees of freedom refer to the number of independent movements a robot can make, such as rotating or translating in different directions.
Mathematical Foundations
The mathematical basis of forward kinematics involves using transformation matrices. These matrices represent the position and orientation of robot links relative to one another. By multiplying these matrices, we can derive the overall transformation from the base of the robot to its end-effector. This process requires a solid understanding of linear algebra and trigonometry.
Practical Applications
Forward kinematics is crucial in robotics applications where the control system needs to know the exact position of the end-effector. For instance, in a robotic arm used for assembly lines, the system must ensure that the arm places components accurately. By calculating forward kinematics, engineers can verify the robot’s movements and make necessary adjustments to ensure precision.
Inverse Kinematics: Finding Joint Parameters
The Challenge of Inverse Kinematics
Inverse kinematics is more challenging than forward kinematics because it involves solving complex equations to find the joint parameters needed to achieve a desired position and orientation of the end-effector. This process is essential for tasks where the robot needs to reach specific targets, such as picking up objects or navigating through a maze.
Analytical and Numerical Solutions
There are two primary methods for solving inverse kinematics problems: analytical and numerical solutions. Analytical solutions involve deriving explicit equations to solve for joint parameters, which is possible for simpler robot configurations. However, for robots with higher degrees of freedom or more complex structures, numerical methods are often employed. These methods use iterative algorithms to approximate the solutions, providing flexibility at the cost of computational complexity.
Applications in Robotics
Inverse kinematics is pivotal in robotics applications requiring precise positioning. For example, in robotic surgery, the surgeon needs the robotic tools to move with extreme accuracy. By solving inverse kinematics, the system can ensure that the robot’s movements align with the surgeon’s commands, enhancing the precision and safety of the procedure.
The Importance of Denavit-Hartenberg Parameters
Standardizing Robot Descriptions
One of the critical challenges in robot kinematics is standardizing how we describe the position and orientation of robot links and joints. The Denavit-Hartenberg (DH) parameters provide a systematic way to represent these transformations using a set of four parameters: link length, link twist, link offset, and joint angle.
Using DH Parameters
By using DH parameters, we can create consistent and concise representations of robot kinematics. This standardization simplifies the process of deriving transformation matrices, making it easier to analyze and control the robot’s movements. DH parameters are particularly useful in complex robots, such as humanoid robots or robotic manipulators with multiple joints.
Practical Implications
In practice, DH parameters enable engineers to develop and simulate robotic systems more efficiently. By standardizing the kinematic descriptions, they can quickly implement and test different configurations, optimizing the robot’s performance for various tasks. This approach also facilitates collaboration and communication among robotics researchers and engineers, as they can use a common framework to describe their systems.
Jacobian Matrix: Relating Velocities
The Role of the Jacobian Matrix
In robot kinematics, the Jacobian matrix is a fundamental tool that relates joint velocities to the end-effector’s linear and angular velocities. This matrix is essential for understanding how changes in joint parameters affect the overall motion of the robot. By analyzing the Jacobian, engineers can predict and control the robot’s behavior more effectively.
Computing the Jacobian Matrix
The Jacobian matrix is derived from the partial derivatives of the position and orientation equations with respect to the joint parameters. This process involves complex mathematical operations, but the resulting matrix provides valuable insights into the robot’s kinematic properties. The Jacobian can be used to identify singularities, where the robot’s movement becomes constrained or undefined.
Applications and Significance
The Jacobian matrix is crucial in applications requiring precise control of the robot’s motion, such as in trajectory planning and optimization. For instance, in robotic welding, the system must ensure that the welding tool follows a specific path with high accuracy. By analyzing the Jacobian, engineers can adjust the robot’s movements to maintain the desired trajectory, improving the quality and efficiency of the welding process.
Trajectory Planning: Moving Smoothly
Defining Trajectory Planning
Trajectory planning involves designing a path for the robot’s end-effector to follow, ensuring smooth and efficient motion. This process is essential in applications where the robot needs to move between points or follow a continuous path, such as in pick-and-place tasks or drawing operations.
Methods of Trajectory Planning
There are several methods for trajectory planning, including point-to-point planning and continuous path planning. Point-to-point planning involves moving the robot between discrete points, while continuous path planning ensures a smooth trajectory between start and end points. These methods can be implemented using various algorithms, such as polynomial interpolation or spline fitting.
Practical Applications
In practical applications, trajectory planning ensures that the robot’s movements are efficient and collision-free. For example, in a manufacturing assembly line, the robot must move components between different stations without interfering with other machines or objects. By planning the trajectory, engineers can optimize the robot’s movements, reducing cycle times and improving overall productivity.
Kinematic Constraints and Singularities
Understanding Constraints
Kinematic constraints are limitations on the robot’s movements, imposed by the design of its joints and links. These constraints can affect the robot’s ability to reach certain positions or perform specific tasks. Understanding and managing these constraints is crucial for effective robot control.
Identifying Singularities
Singularities are specific configurations where the robot’s movement becomes undefined or constrained. These occur when the Jacobian matrix loses rank, resulting in a loss of control over certain degrees of freedom. Singularities can pose significant challenges in robot kinematics, as they can lead to unpredictable or unstable movements.
Managing Constraints and Singularities
To manage kinematic constraints and singularities, engineers must carefully design the robot’s structure and control algorithms. This involves analyzing the robot’s kinematic properties and identifying potential issues during the design phase. By addressing these challenges early, engineers can ensure that the robot operates smoothly and reliably in various scenarios.
Practical Applications of Robot Kinematics
Industrial Robots
In industrial settings, robot kinematics is fundamental to the design and control of robotic arms used for assembly, welding, painting, and material handling. These robots must move with precision and repeatability to ensure high-quality output. By understanding and applying kinematic principles, engineers can optimize the performance of industrial robots, enhancing efficiency and productivity.
Medical Robots
Medical robots, such as surgical robots, rely heavily on kinematics to perform delicate and precise tasks. These robots assist surgeons in procedures that require high accuracy, such as minimally invasive surgeries. By solving kinematic equations, the robotic system can translate the surgeon’s movements into precise actions, improving the safety and effectiveness of medical procedures.
Service Robots
Service robots, designed for tasks such as cleaning, delivery, and customer assistance, also benefit from advanced kinematic analysis. These robots must navigate complex environments and interact with various objects and people. By applying kinematic principles, engineers can develop robots that move smoothly and adapt to changing conditions, enhancing their usability and reliability.
Humanoid Robots
Humanoid robots, designed to mimic human movements and interactions, present unique kinematic challenges. These robots must coordinate multiple joints and limbs to achieve lifelike movements. By studying humanoid kinematics, researchers can develop algorithms that enable these robots to walk, grasp objects, and perform other tasks with a high degree of realism and functionality.
Future Trends in Robot Kinematics
Advancements in Computational Methods
As computational power continues to increase, more sophisticated algorithms and methods for solving kinematic equations are being developed. These advancements enable the design and control of robots with higher degrees of freedom and more complex structures. Future trends in robot kinematics will likely involve leveraging artificial intelligence and machine learning to optimize robot movements and improve their adaptability.
Integration with Artificial Intelligence
The integration of kinematics with artificial intelligence (AI) is a promising area of research. By combining kinematic models with AI algorithms, robots can learn and adapt to their environments more effectively. This approach can enhance the robot’s ability to perform tasks autonomously, improving their efficiency and effectiveness in dynamic and unstructured environments.
Development of Soft Robotics
Soft robotics is an emerging field that focuses on designing robots with flexible and compliant materials. These robots can adapt to their surroundings and perform delicate tasks that traditional rigid robots cannot. Kinematics in soft robotics involves studying the deformation and movement of these materials, presenting unique challenges and opportunities for innovation.
Enhancements in Human-Robot Interaction
Improving human-robot interaction (HRI) is a critical focus area for future robot kinematics. Robots need to understand and predict human movements to interact safely and effectively. By integrating kinematic models with advanced sensors and AI, robots can become more intuitive and responsive, enhancing their ability to collaborate with humans in various settings.
Conclusion: The Importance of Understanding Robot Kinematics
Robot kinematics is a foundational aspect of robotics, essential for designing, controlling, and optimizing robotic systems. Whether in industrial automation, medical applications, or service robots, understanding kinematics enables engineers to develop robots that move precisely and efficiently. By mastering the principles of forward and inverse kinematics, the use of DH parameters, and the significance of the Jacobian matrix, we can create more advanced and capable robotic systems.
The future of robot kinematics is bright, with ongoing advancements in computational methods, AI integration, soft robotics, and human-robot interaction. As these technologies evolve, we can expect robots to become even more versatile and integrated into our daily lives, performing tasks with greater autonomy and adaptability.
Disclaimer
The information provided in this blog is for educational purposes only. While we strive for accuracy, some details may change as the field of robotics advances. Please report any inaccuracies so we can correct them promptly.